Enhance quality management with an integrated QMS solution
Drive consistency and continuous improvement across operations.
%20Graphic.png?width=1135&height=651&name=Quality%20Management%20(QMS)%20Graphic.png)
Ensure Product Excellence
Improve business operations through a quality management system.
Reduce Defects
The cost of poor quality can exceed 10% of revenue. Identify defects early, improving product quality and customer satisfaction.
Enhance Product Consistency
Manufacturers with robust quality management systems are 50% more likely to meet product specifications consistently, reducing rework and returns.
Boost Operational Efficiency
Companies with automated quality processes see a 30% reduction in downtime, ensuring smoother production cycles and higher throughput.
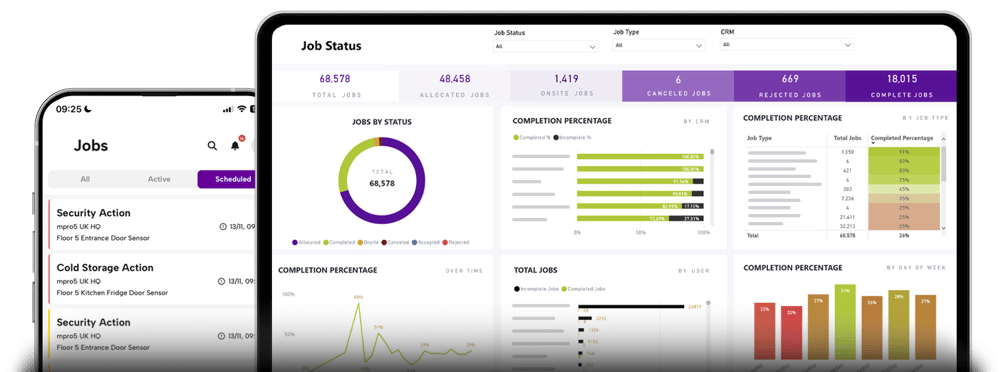
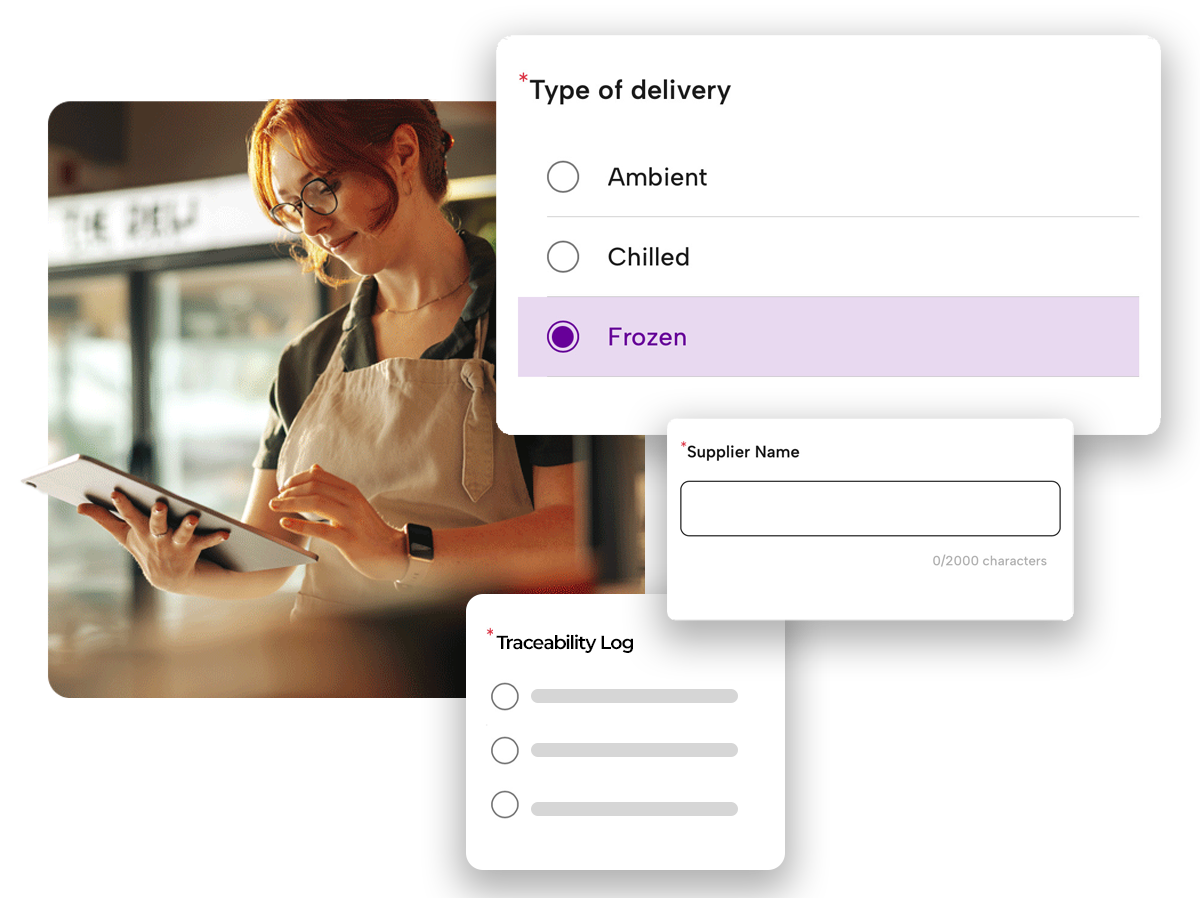
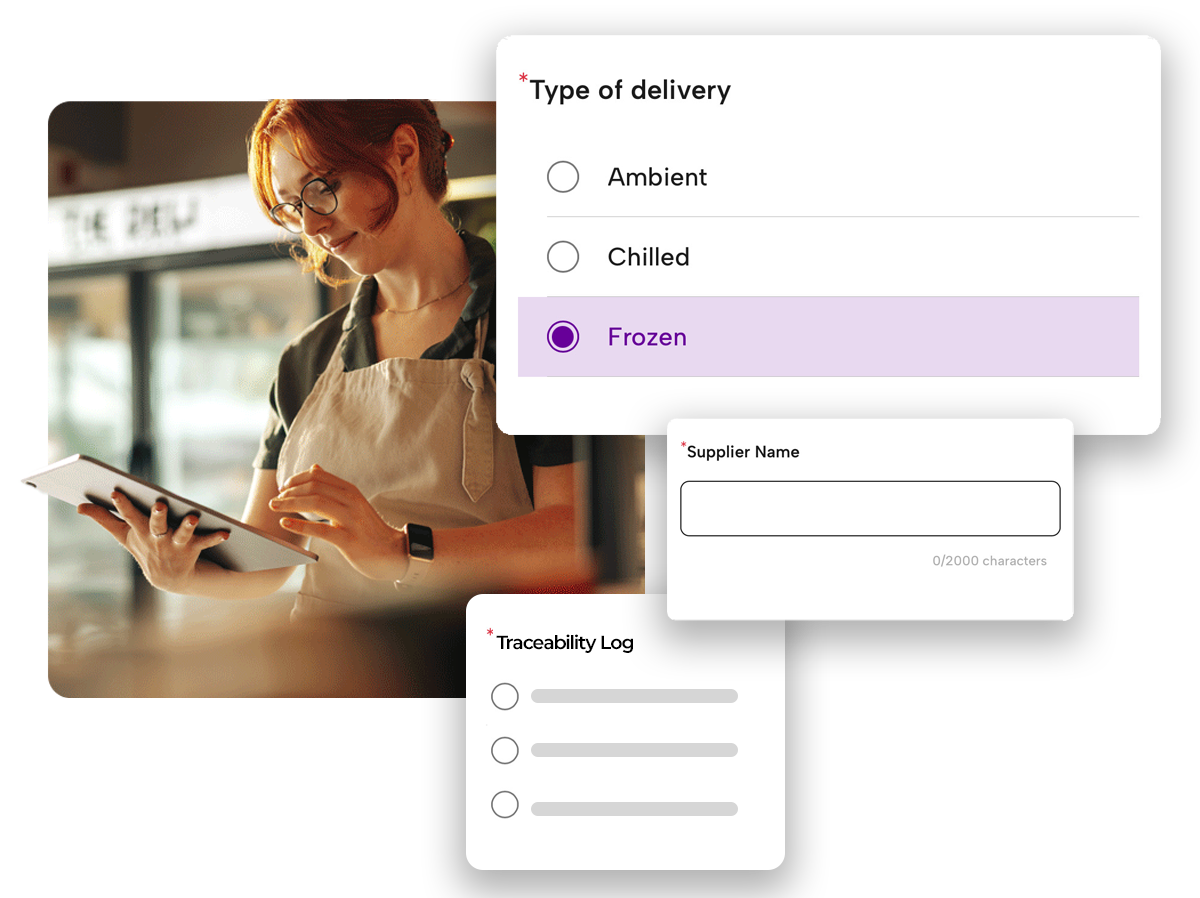
Make Informed, Data-Driven Decisions
Leverage real-time analytics to improve quality control.
Learn More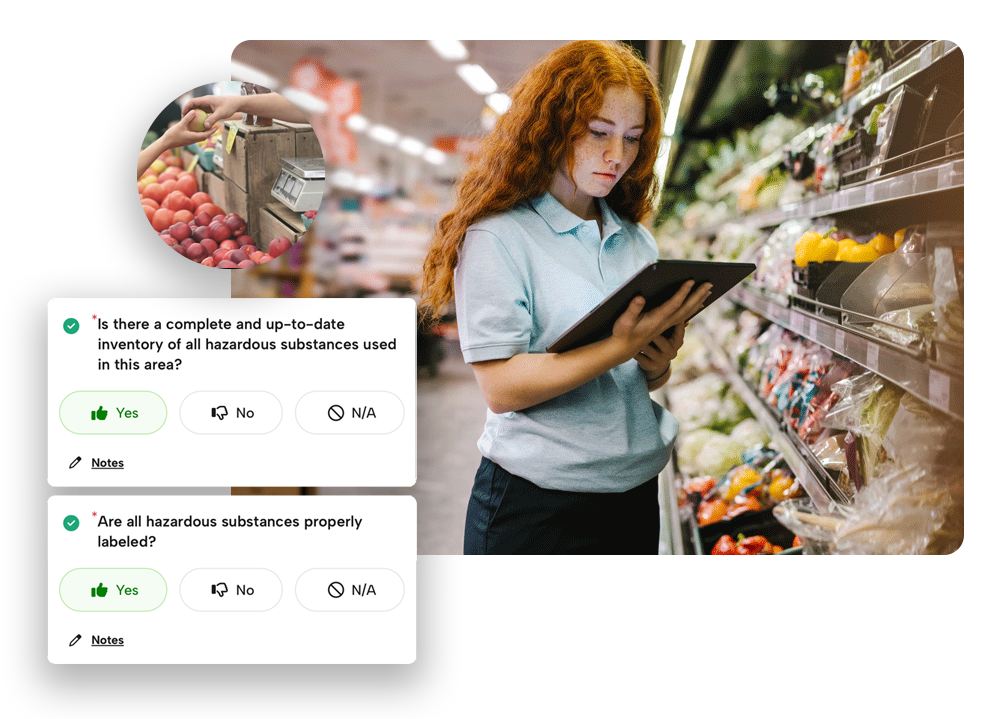
Gain actionable insights from detailed data analytics, allowing you to proactively identify defects, track performance trends, and optimize processes. By making data-driven decisions, you can improve product quality, reduce waste, and enhance operational efficiency, ensuring higher customer satisfaction.
Centralize Quality Data and Communication
Streamline communication and documentation for better collaboration.
Learn More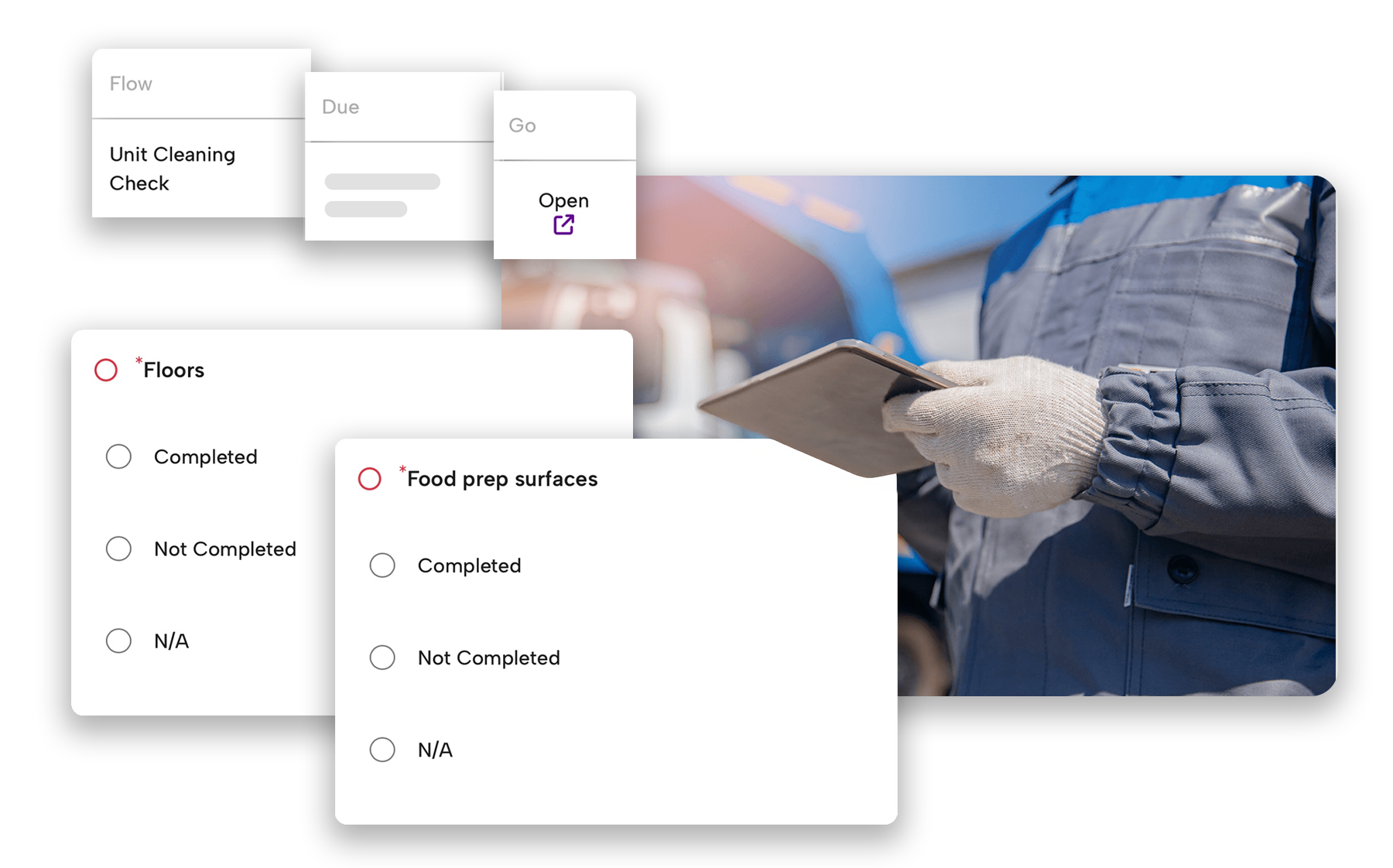
Consolidate all quality management data, including inspection reports, compliance records, and corrective actions, into one platform. A unified solution ensures that your team and stakeholders are always on the same page, improving transparency, reducing errors, and enhancing collaboration.
Eliminate Paper-Based Processes
Digitize your quality management system for greater efficiency.
Learn More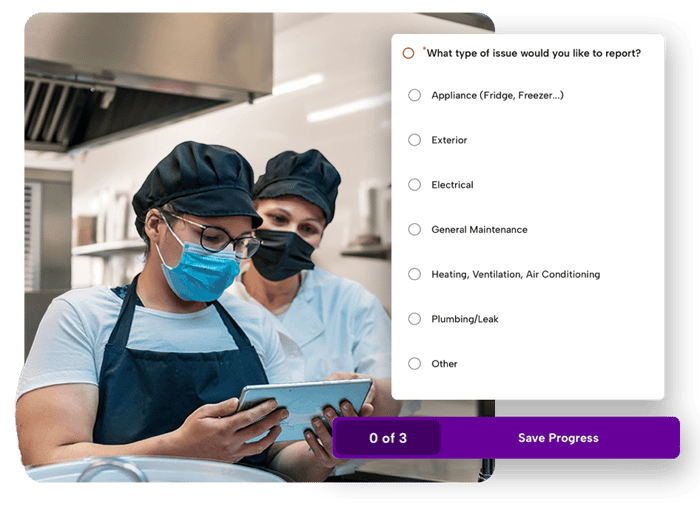
Transition from paper-based quality control systems to a digital platform that stores all data in real-time. A digital solution enhances traceability, reduces the risk of errors, and improves the speed of reporting and compliance tracking, ultimately driving a higher standard of product quality.
Start streamlining your processes today!
Complete the short form below and we'll be in touch soon!
43%
UK supermarkets using mpro5
140+
Million work orders completed
175+
Million jobs created
Explore All of our Food Safety Solutions:
Select an option below:
- HACCP
- Food Safety Management
- Compliance
- Food Traceability
- Temperature Checks
- Operations Management
- OHS
HACCP
Take the risk out of food safety with digitized HACCP planning. Proactively identify, prevent, and control potential hazards.
Food Safety Management
Simplify food safety management for compliance and quality. Protect your brand with the highest safety standards.
Temperature Checks
Streamline temperature monitoring for safety and compliance. Eliminate risks with automated, real-time automated logging.
Operations Management
Transform operations management with mpro5's intuitive solutions. Streamline workflows and drive operational excellence across your organization.
OHS
Protect your people and business with comprehensive OHS tools. Ensure compliance and foster a safe, productive environment.

Frequently Asked Questions
Find answers to common questions we receive.
-
What is a Quality Management System (QMS)?
A Quality Management System (QMS) is a set of policies, processes, and procedures used by organizations to ensure they consistently meet customer expectations and regulatory requirements. A QMS provides a systematic approach to managing quality control and assurance, leading to improved products, services, and customer satisfaction.
-
Why is a QMS important for businesses?
A QMS is essential for businesses to consistently meet quality standards, improve operational efficiency, and drive customer satisfaction. It helps organizations streamline processes, reduce waste, increase compliance, and foster continuous improvement. A robust QMS can lead to better product quality, cost savings, and stronger customer loyalty.
-
How does a Quality Management System work?
A Quality Management System works by organizing an organization's processes and resources to maintain and improve product and service quality. It involves activities such as defining quality policies, setting quality objectives, monitoring performance, conducting audits, and improving processes based on data-driven insights.
-
What are the benefits of using a Quality Management System (QMS)?
The key benefits of using a QMS include:
- Improved Quality Control: Standardize and automate quality inspections and processes to minimize defects and improve consistency.
- Operational Efficiency: Streamline workflows and reduce waste by automating key processes.
- Better Compliance and Risk Management: Easily maintain records for audits and ensure compliance with industry regulations.
- Enhanced Customer Satisfaction: Deliver products and services that consistently meet or exceed customer expectations, strengthening brand loyalty.
With solutions like mpro5, businesses gain enhanced capabilities such as custom workflows, real-time monitoring, and easy integration with other systems to ensure the highest level of quality across operations.
-
How does mpro5 enhance Quality Management?
mpro5 provides a robust solution for quality management by offering features like:
- Automated Quality Workflows: Simplify and automate quality inspections, reporting, and corrective actions.
- Real-Time Data: Use real-time data to monitor quality metrics and identify issues before they escalate.
- Customizable Templates: Tailor forms, reports, and workflows to your specific quality management needs.
- Seamless Integration: Integrate with other business systems to centralize quality data, ensuring consistent information across departments.
Our latest insights:
3 min read
Ensuring Compliance in the Food Industry: Strategies for Channel Partners and Industry Leaders
Dec 6, 2024 by Matt Smith
Businesses must ensure they are compliant with Natasha’s Law amid continued allergen woes
Dec 2, 2024 by Matt Smith